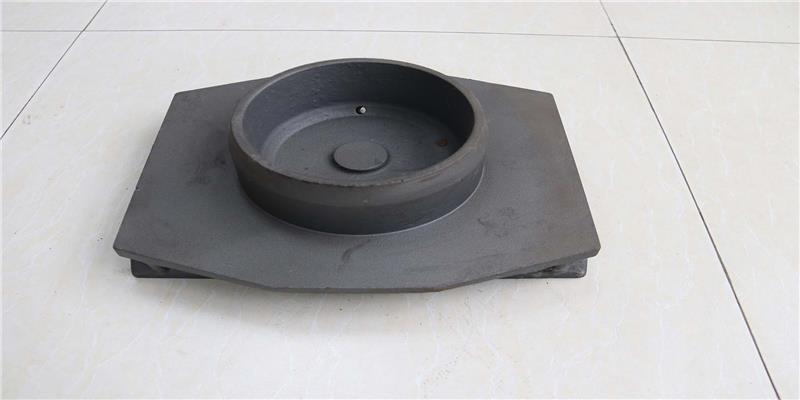
安徽偉工機械科技有限公司
經營模式:生產加工
地址:蕪湖縣機械工業(yè)園榆林路1388號
主營:電渦流緩速器組件,車輛配件,閥門及配件,工業(yè)管道配件研發(fā)
業(yè)務熱線:1386-8888645
QQ:1353026929
精鑄生產中產生的粉塵主要為金屬碎屑、非金屬顆粒、碎鋼丸和型殼在零件上剝離產生的細砂粉末。
精密鑄造在拋光過程中,產生的粉塵主要為金屬粉塵,當金屬積累到后的與明火或者溫度的碰撞,會引發(fā)安全隱患,不僅危機工人的生命安全,更是將工廠毀于一旦。
應用傳統(tǒng)的除塵方法會隨設備的老化,消除不及時或瞬間產生太多粉塵而不能完全去除,漂浮在空氣中,嚴重影響工作環(huán)境,給安全生產帶來隱患。
根據精密鑄造廠情況,設計以下兩種除塵方案:
局部排風系統(tǒng)設計
排風集中在產生粉塵的局部地點設置捕集設置,將粉塵排走,以控制粉塵在室內擴散,用新鮮空氣把整個車間粉塵濃度稀釋到zui低,這種方式成本低,但治標不治本。
整體除塵治理法
針對鑄造粉塵產生點進行、收集、凈化,投資少,凈化效果好。鑄造行業(yè)防塵、除塵要綜合治理的方法,為防止各工部之間相互污染,必須對產生粉塵、廢氣的各個生產工序都進行治理。
如對于極易產生粉塵的混砂工藝、沖天爐熔煉工藝、機械振動落砂工藝及人工清砂工藝等皆應采取嚴格的防塵、除塵措施。
對生產過程的舊砂回收、再生輸送工藝和設備,對開箱、除砂、噴拋丸鑄件清理工藝和設備,對原料及廢砂的運輸、收集過程和設備等,都應配置相適應的防塵、除塵措施。





熔模鑄造的制模工藝
按照模料的規(guī)定成分和配比,將各種原料熔融成液態(tài),混合并攪拌均勻,濾去雜質澆制成糊狀模料,即可以壓制熔模。壓制熔模普遍采用壓制成型的辦法。該方法允許使用液態(tài)、半液態(tài)以及固態(tài)、半固態(tài)模料。液態(tài)和半液態(tài)模料在低的壓力下壓制成型,稱為壓注成型;半固態(tài)或固態(tài)模料在高的壓力下壓制成型,稱為擠壓成型。無論是壓注成型還是擠壓成型,都必須考慮充填和凝固時的優(yōu)缺點。
(1)壓注成型
壓注成型的注蠟溫度多在熔點以下,此時模料是液、固兩相共存的漿狀或糊狀。呈漿狀的模料中,液相量顯著超過固相量,所以仍保留著液體的流動性。在這種狀態(tài)下壓注,熔模表面具有較低的粗糙度,而且不易出現由于紊流、飛濺帶來的表面缺陷。糊狀模料的溫度比漿狀模料更低,已失去流動性,雖少有表面缺陷,但卻具有較高的表面粗糙度。
模料壓注成型時,在保證良好充填情況下應盡量采用低的模料溫度和壓型工作溫度。壓力的選擇并不是越大越好,雖然壓力大熔模收縮率小,但壓力和壓注速度過大,會使熔模表面不光滑,產生“鼓泡”(熔模表皮下氣泡膨脹),同時,使模料飛濺出現冷隔缺陷。在制模過程中,為了避免模料粘附壓型,提高熔模表面光潔度,應使用分型劑,特別是對于松香基模料。
(2)擠壓成型
擠壓成型把在低溫塑性狀態(tài)下的模料擠壓入型腔,在高壓下成型,以減少和防止熔模收縮。擠壓成型時的模料處于半固態(tài)或固態(tài),該模料在正常條件下比較硬,但在高壓下能夠流動,其特點是粘度大。因此擠壓時壓力的大小取決于模料的粘度及在注料孔和型腔中的流動阻力。模料的粘度愈大,注料孔徑愈小,型腔尺寸愈大而橫截面積愈小以及模料行程愈長,則模料流動時的阻力愈大,因此需要愈高的擠壓壓力。采用半固態(tài)模料擠壓成型,熔模的凝固時間縮短,因而生產率,特別適用于生產具有厚大截面的鑄件。
不銹鋼精密鑄造可由實型法或陶瓷型殼法生產。實型法是用細的硅膠涂料先在一次性的模樣上涂刷一層,再撒上耐火沙子,然后在模樣周圍灌以漿料,并讓其凝固。模樣因為沒有分型面,所以所有尺寸公差都保證一定的精度。震動砂箱使模樣周圍的漿料密實而無氣泡,并使水和固體材料分離,由型箱上部排出。將沙箱倒置在烘爐中使蠟模熔化蠟液流出,即剩下鑄型。鑄型在高溫下進行焙燒,熔燒后當鑄型還處在熱狀態(tài)即準備進行澆注。鑄型按垂直方式排列,通常采用重力澆注,有時也采用離心、真空或大氣壓力的方法,在熱的鑄型中進行澆注。澆注完畢后,使鑄型冷卻,然后破壞鑄型取出鑄件?!?
陶瓷殼型鑄造由于制作鑄型的費用較實型鑄造法便宜,這已被證實對精密鑄造生產者是有利的。精鑄法的模樣是用蠟模在中心直澆口棒上。經組成好的模組在合適的溶劑中仔細清洗,浸入硅酸乙酯中滴流幾分鐘。停止滴流后,將模組放入流態(tài)床中涂刷熔融過的石英砂涂刷,一般涂刷5層就足夠了。陶瓷殼型鑄造占所有精密鑄件的85%以上。
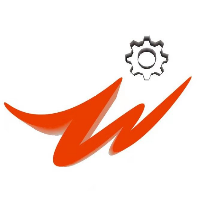
張經理先生
手機:18949552994